Predictive Maintenance in Manufacturing with Blue Yonder
A single unexpected equipment failure can halt production lines, disrupt supply chains, and lead to cascading financial losses. The traditional approach to maintenance—either reactive (fixing issues after failure) or preventive (scheduled servicing regardless of need)—often falls short of delivering the agility and efficiency manufacturers require today.
This is where predictive maintenance, powered by advanced analytics and AI-driven insights, is transforming the industry. By leveraging data science and machine learning, manufacturers can anticipate failures before they happen, optimize maintenance schedules, and significantly reduce operational disruptions. Blue Yonder, a leader in end-to-end supply chain solutions, offers a robust predictive maintenance solution that empowers manufacturers to shift from a reactive stance to a proactive, data-driven strategy.
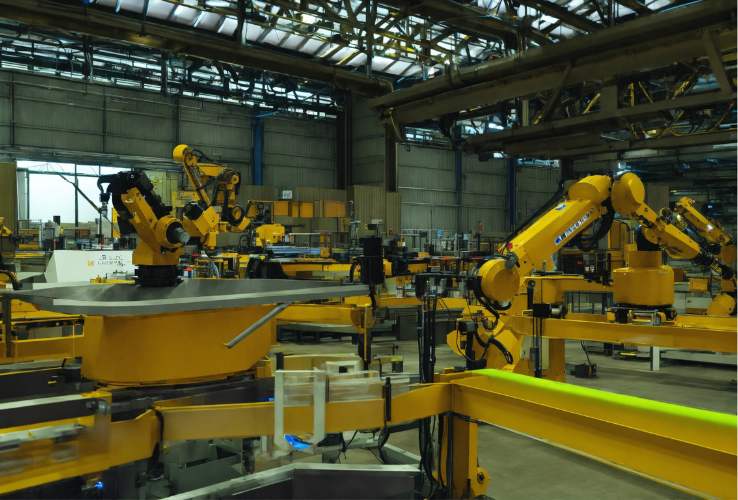
The High Cost of Downtime: Why Predictive Maintenance Matters
Manufacturers operate in an environment where efficiency is paramount. A McKinsey report estimates that unplanned downtime costs industrial manufacturers an average of $50 billion annually. Traditional maintenance models, while effective to an extent, lack precision. Preventive maintenance often results in unnecessary servicing and parts replacement, driving up costs, while reactive maintenance can lead to prolonged downtime and reduced asset lifespan.
Predictive maintenance eliminates these inefficiencies by applying AI and IoT-driven monitoring to predict equipment failures with remarkable accuracy. Blue Yonder’s solution integrates seamlessly with manufacturing operations, utilizing real-time sensor data, historical performance trends, and advanced analytics to provide actionable insights. The result? Lower maintenance costs, improved asset longevity, and enhanced operational reliability.
How Blue Yonder’s Predictive Maintenance Works
At the core of Blue Yonder’s predictive maintenance solution is a sophisticated machine learning engine that continuously analyzes data from manufacturing equipment. By capturing and processing signals such as vibration patterns, temperature fluctuations, pressure deviations, and historical failure data, the system can detect anomalies that indicate potential failures.
- Real-Time Data Ingestion – Blue Yonder’s platform aggregates data from industrial sensors, IoT-enabled machines, and enterprise systems to create a holistic view of equipment health.
- AI-Driven Anomaly Detection – Machine learning models identify deviations from normal operating behavior, flagging potential risks before they escalate into failures.
- Prescriptive Insights & Automated Actions – The system doesn’t just predict failures; it also recommends optimal maintenance actions. This could mean adjusting operational parameters, scheduling targeted repairs, or notifying maintenance teams before breakdowns occur.
- Seamless ERP & MES Integration – The solution integrates with Enterprise Resource Planning (ERP) and Manufacturing Execution Systems (MES), ensuring that predictive maintenance aligns with broader production schedules and resource planning.
Strategic Benefits for Manufacturers
For manufacturers operating in highly competitive and asset-intensive industries, predictive maintenance delivers significant advantages:
1. Reduced Downtime and Increased Uptime
Predictive analytics-driven maintenance reduces unplanned downtime by up to 50%, ensuring that production lines remain operational with minimal disruptions.
2. Optimized Maintenance Costs
With a predictive approach, manufacturers only perform maintenance when it’s truly needed. This leads to cost savings on spare parts, labor, and unplanned operational halts. According to a Deloitte study, predictive maintenance can lower maintenance costs by 25-30% compared to traditional approaches.
3. Extended Asset Lifespan
By continuously monitoring equipment conditions and addressing issues early, manufacturers can extend the operational life of machinery, reducing capital expenditures on replacements.
4. Enhanced Supply Chain Resilience
In industries where supply chain synchronization is critical, avoiding unexpected equipment failures helps maintain consistent production flows, preventing ripple effects across the supply chain.
5. Sustainability & Energy Efficiency
Predictive maintenance also contributes to sustainability goals by improving energy efficiency and reducing material waste. Equipment running at optimal conditions consumes less power and generates fewer emissions, supporting corporate ESG initiatives.
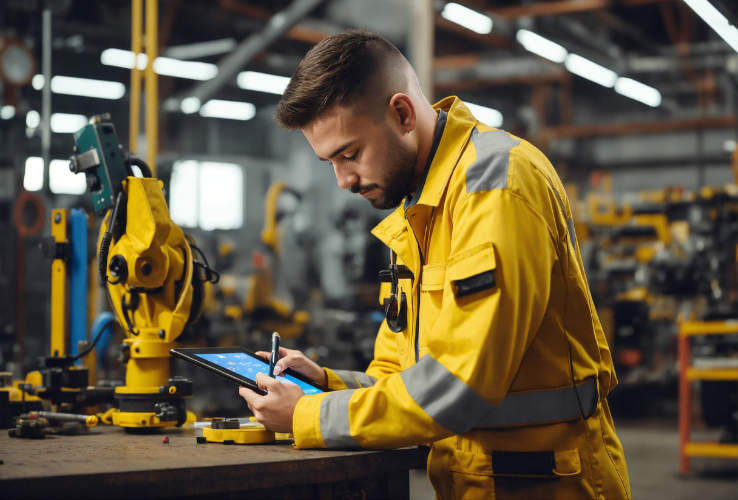
Industry Adoption: The Competitive Edge of AI-Driven Maintenance
Leading manufacturers in automotive, aerospace, industrial equipment, and consumer goods are already leveraging AI-powered predictive maintenance to enhance their operations. Companies that embrace this shift are gaining a competitive advantage, reducing operational risks, and unlocking new levels of efficiency.
Blue Yonder’s predictive maintenance solution is designed to scale across multiple manufacturing environments, making it an ideal choice for global enterprises looking to standardize maintenance strategies across multiple production sites.
The Future of Maintenance: Proactive, AI-Driven, and Scalable
The next evolution of predictive maintenance will integrate even deeper with edge computing, digital twins, and autonomous maintenance systems. As AI models become more sophisticated, they will not only predict failures but self-correct minor inefficiencies in real-time, further enhancing reliability and performance.
For manufacturers aiming to stay ahead of disruption, adopting predictive maintenance isn’t just an efficiency play—it’s a strategic imperative. With Blue Yonder, enterprises can transform maintenance from a cost center to a value driver, ensuring resilience, efficiency, and long-term competitiveness.