Circular Economy in Manufacturing: Tech-Enabled Sustainability
In a world grappling with resource scarcity, environmental degradation, and rising consumer consciousness, the manufacturing sector stands at a crossroads. The traditional linear model of “take, make, dispose” is no longer sustainable. Instead, manufacturers are turning to the circular economy—a system designed to eliminate waste and keep resources in use for as long as possible. This shift isn’t just an ethical imperative; it’s a strategic transformation driven by technology and innovation.
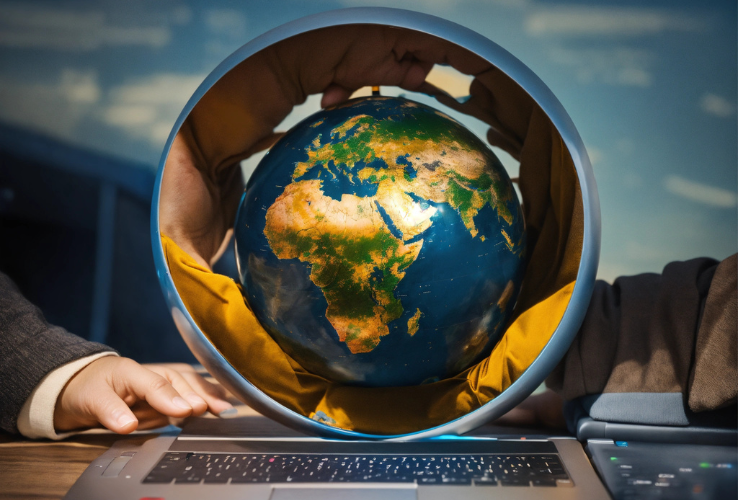
The Need for a Circular Economy in Manufacturing
Global manufacturing consumes vast amounts of raw materials and generates significant waste, contributing to environmental challenges like resource depletion, greenhouse gas emissions, and pollution. With increasing regulatory pressures, rising raw material costs, and growing demand for sustainable products, the transition to a circular economy is not just desirable—it’s essential.
The circular economy reimagines manufacturing processes by focusing on resource efficiency, product longevity, and waste minimization. This approach not only benefits the planet but also enhances business resilience by reducing dependency on finite resources and fostering innovation.
How Technology is Driving the Circular Economy
Technology serves as the backbone of the circular economy, enabling manufacturers to re-engineer processes, track resources, and optimize operations. Here’s how:
1. Digital Twin Technology
Digital twins—virtual replicas of physical assets—enable manufacturers to simulate, monitor, and optimize production processes in real time. By providing insights into wear and tear, energy consumption, and inefficiencies, digital twins help extend the lifespan of equipment and reduce waste.
For example, Siemens uses digital twins in its factories to optimize resource usage and improve energy efficiency. These insights allow manufacturers to predict maintenance needs, reducing downtime and extending the operational life of machinery.
2. IoT and Smart Sensors
The Internet of Things (IoT) plays a critical role in resource tracking and optimization. Smart sensors embedded in manufacturing equipment can monitor material usage, energy consumption, and waste generation. This data helps identify inefficiencies, enabling manufacturers to make informed decisions about process improvements.
In industries like automotive, IoT-enabled systems track the lifecycle of components, ensuring they can be recovered, refurbished, or recycled at the end of their use.
3. Advanced Recycling Technologies
Traditional recycling methods often struggle with efficiency and quality. However, advancements in chemical recycling and AI-driven sorting technologies are changing the game. These innovations can break down complex materials into their basic components, allowing for higher-quality recycled inputs.
For instance, chemical recycling processes are now being used to convert plastic waste into raw materials that can be reused in manufacturing, creating a closed-loop system.
4. Blockchain for Traceability
Blockchain technology ensures transparency and traceability across the supply chain, a critical requirement for circular systems. By securely recording data about materials, components, and products, blockchain enables manufacturers to verify the origin, composition, and lifecycle of goods.
Companies like IBM are leveraging blockchain to create circular supply chains, ensuring that materials are responsibly sourced and can be efficiently recycled or repurposed.
Practical Applications in Circular Manufacturing
Product Design for Longevity and Reuse
Manufacturers are adopting design principles that prioritize durability, modularity, and recyclability. By designing products that can be easily disassembled, repaired, or upgraded, they extend product lifecycles and reduce waste. For example, modular smartphones allow consumers to replace individual components rather than discarding the entire device.
Industrial Symbiosis
In a circular economy, waste from one manufacturing process becomes a resource for another. This concept, known as industrial symbiosis, is gaining traction in sectors like energy and chemicals. For instance, excess heat from one factory might be used to power another facility nearby, reducing overall energy consumption.
Closed-Loop Supply Chains
Leading manufacturers are implementing closed-loop supply chains, where used products are collected, refurbished, and resold. This approach is particularly popular in the electronics and automotive sectors, where end-of-life components can be recycled into new products. Companies like Dell and BMW have embraced this model, creating circular systems for laptops and car batteries.
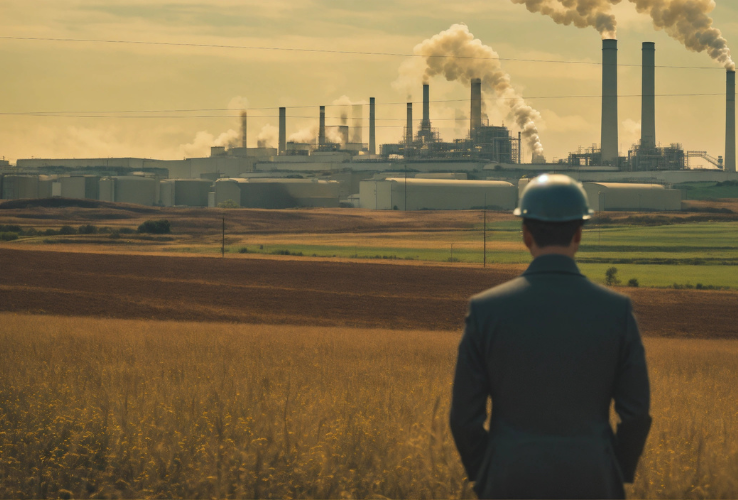
Benefits of a Circular Economy for Manufacturers
- Cost Savings: By minimizing waste and maximizing resource efficiency, manufacturers can significantly reduce costs associated with raw materials and waste disposal.
- Regulatory Compliance: Transitioning to circular practices helps businesses meet increasingly stringent environmental regulations, avoiding fines and reputational risks.
- Competitive Advantage: Consumers are increasingly choosing sustainable brands. Circular economy initiatives enhance brand loyalty and attract environmentally conscious customers.
- Innovation: Circular practices drive innovation by encouraging companies to rethink product design, materials, and supply chains.
Overcoming Challenges
While the circular economy offers immense potential, it comes with challenges. High upfront costs, lack of infrastructure, and resistance to change are common barriers. Manufacturers must also invest in workforce training to ensure that employees understand and embrace new processes and technologies.
Collaboration is critical to overcoming these obstacles. Governments, industry bodies, and tech providers must work together to create supportive ecosystems, provide funding for innovation, and establish clear guidelines for circular practices.
The Path Forward
The circular economy is more than a sustainability initiative; it’s a strategic advantage for manufacturers ready to embrace the future. By leveraging technology to optimize resources, reduce waste, and create closed-loop systems, manufacturers can unlock new levels of efficiency and resilience.
As the shift toward circularity gains momentum, manufacturers must act decisively. Those who adopt these principles early will not only lead the way in sustainable innovation but also build stronger, more adaptable businesses that thrive in a resource-constrained world.
The journey to a circular economy requires vision, investment, and collaboration, but the rewards—both for the planet and for the bottom line—make it a path worth pursuing.