Smart Factories and Industry 4.0: Redefining Modern Manufacturing
Why Smart Factories Matter
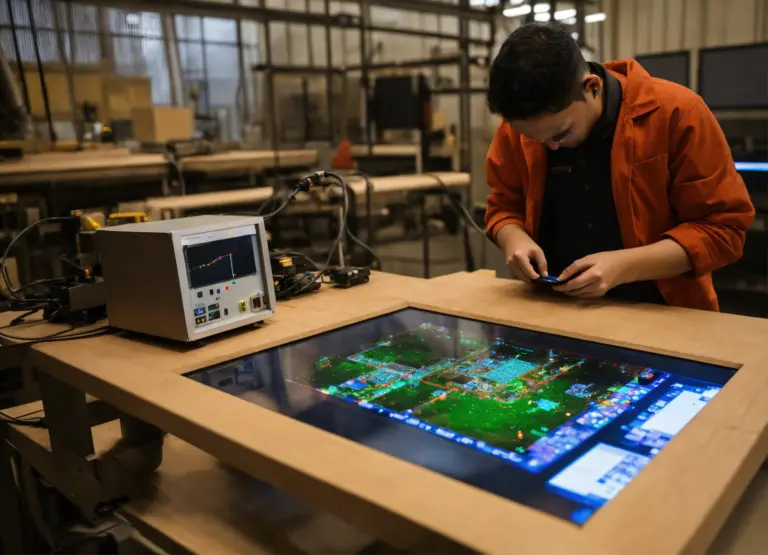
Smart factories embody the principles of Industry 4.0, where advanced automation and interconnected systems drive innovation in manufacturing. By integrating robotics, IoT, AI, and real-time analytics, they enhance efficiency, precision, and sustainability. Businesses adopting smart factory strategies are better positioned to meet evolving consumer demands, optimize operations, and stay competitive in a rapidly advancing industrial landscape.
Key Components of Smart Factories
Smart factories represent the pinnacle of modern manufacturing, blending advanced technologies to create highly efficient, adaptive, and interconnected production environments. By integrating digital tools such as IoT, AI, and robotics, these factories enhance productivity, ensure precision, and enable real-time decision-making. They are designed to respond dynamically to changes in demand, streamline workflows, and optimise resource utilisation. Below are the essential components that form the foundation of smart factories and drive their transformative capabilities:
Automation and Robotics
Automated machinery and robotics improve production efficiency, reduce errors, and enhance worker safety by handling repetitive or hazardous tasks.IoT and Connected Systems
IoT devices enable seamless communication between machines, sensors, and systems, fostering real-time data sharing and coordinated operations.AI and Machine Learning
AI-driven systems predict equipment failures, optimize production schedules, and provide actionable insights for decision-making.Digital Twins
Virtual replicas of physical systems allow manufacturers to simulate, monitor, and optimize processes without disrupting operations.Sustainability Practices
Automation supports eco-friendly manufacturing with energy-efficient systems, waste reduction, and optimized resource utilization.
How to Implement Industry 4.0 Strategies
Implementing Industry 4.0 strategies involves integrating advanced technologies and reimagining traditional processes to build smart, interconnected systems across manufacturing and business operations. This transformation requires a combination of innovative tools, robust data infrastructure, and a workforce ready to embrace digital advancements. From leveraging IoT and AI to fostering collaboration and ensuring cybersecurity, successful implementation hinges on a strategic approach tailored to specific business needs. Below are key steps to effectively transition to Industry 4.0:
Adopt Advanced Technologies
Invest in AI, IoT, robotics, and cloud platforms to modernize manufacturing processes. Ensure compatibility and scalability for future expansions.Leverage Predictive Analytics
Use real-time data and AI tools to anticipate maintenance needs, prevent downtime, and streamline production cycles.Integrate Supply Chains
Connect supply chain systems with smart factory operations for efficient inventory tracking, just-in-time manufacturing, and improved logistics.Empower the Workforce
Upskill employees to work with advanced technologies and foster collaboration between human expertise and automated systems.Focus on Cybersecurity
Protect interconnected systems and sensitive data with robust cybersecurity measures, encryption, and compliance with industry standards.
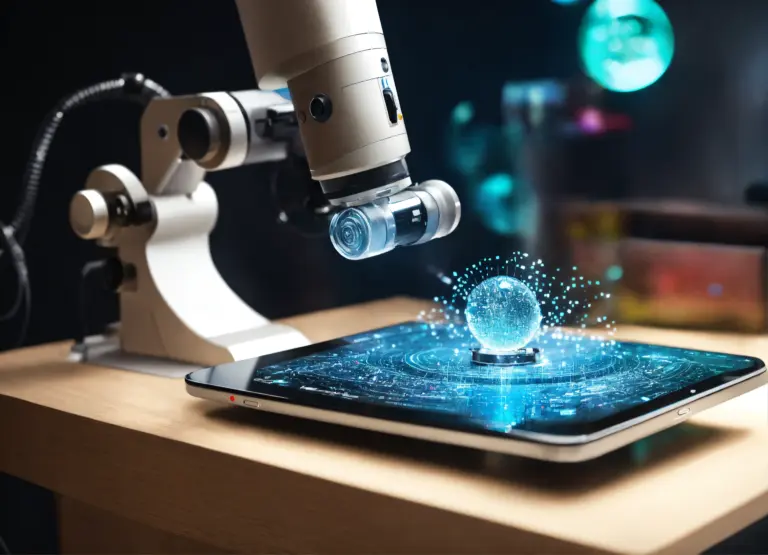
Emerging Technologies Driving Smart Factories
Smart factories are at the forefront of the manufacturing revolution, powered by cutting-edge technologies that enable automation, efficiency, and real-time adaptability. These technologies, ranging from artificial intelligence to advanced robotics, are reshaping production processes and fostering innovation across industries. By integrating these advancements, smart factories achieve unparalleled precision, scalability, and sustainability. Below are the emerging technologies that are driving the evolution of smart factories and redefining the future of manufacturing:
Artificial Intelligence (AI)
Enhances operational efficiency with intelligent decision-making, predictive analytics, and automation of complex tasks.Internet of Things (IoT)
Facilitates communication between devices and systems, enabling real-time monitoring and adaptive manufacturing processes.5G Connectivity
Supports high-speed data transmission for seamless integration of IoT devices and real-time operational control.Blockchain Technology
Enhances supply chain transparency and ensures the authenticity of materials, reducing risks and inefficiencies.Augmented Reality (AR)
AR tools assist in training, maintenance, and quality control by overlaying digital information on physical systems.
Benefits of Smart Factories
Smart factories are revolutionising manufacturing by leveraging advanced technologies to create intelligent, adaptive, and highly efficient production systems. These factories offer a range of benefits, from improving operational efficiency and reducing costs to enhancing product quality and enabling real-time decision-making. By integrating automation, data analytics, and connected systems, smart factories empower businesses to respond swiftly to market demands, optimise resource utilisation, and achieve greater sustainability. Below are some of the key benefits driving the adoption of smart factory solutions:
Increased Efficiency
Automation reduces production times and minimizes waste, leading to higher output and better resource utilization.Enhanced Product Quality
Precision and consistency in automated systems ensure superior product quality with fewer defects.Cost Optimization
Predictive maintenance and streamlined operations reduce operational costs and increase profitability.Sustainability and Compliance
Eco-friendly practices and adherence to regulations improve brand reputation and align with global sustainability goals.
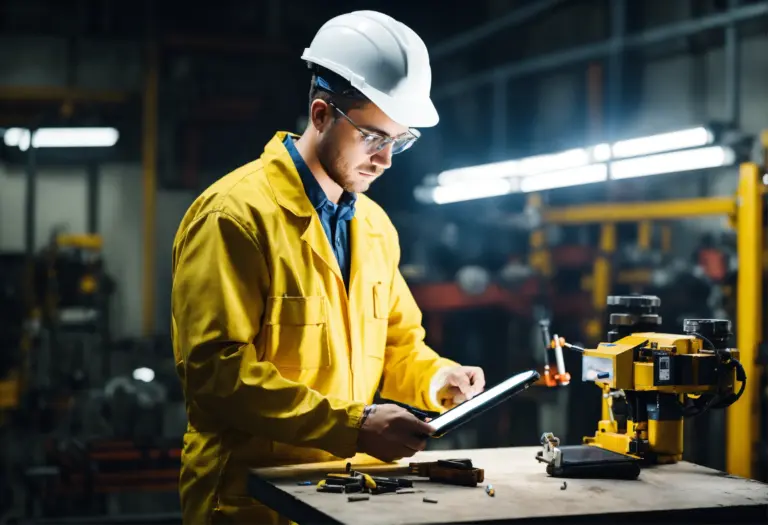
Challenges in Adopting Smart Factories
While smart factories offer immense potential to revolutionise manufacturing, their adoption comes with significant challenges. Transitioning to a smart factory requires substantial investments in technology, infrastructure, and workforce training. Businesses must address concerns like integration with legacy systems, data security, and the complexity of implementing interconnected technologies. Additionally, the lack of standardisation and skilled personnel can hinder seamless adoption. Below are some of the key challenges faced by organisations in implementing smart factory initiatives:
Integration with Legacy Systems
Transitioning from traditional setups to smart factory systems requires time, expertise, and investment.High Initial Costs
Implementing advanced technologies involves significant upfront expenses, which may deter smaller manufacturers.Data Security Risks
Interconnected systems are vulnerable to cyber threats, necessitating robust security frameworks.Workforce Adaptation
Upskilling employees to work with new technologies is essential but can be time-consuming and costly.
Trends Shaping the Future of Manufacturing
The manufacturing industry is undergoing a profound transformation, driven by technological advancements and evolving market demands. Emerging trends such as automation, artificial intelligence, and sustainable practices are redefining production processes, enhancing efficiency, and creating new opportunities for innovation. As manufacturers embrace digitalisation and smart technologies, they are building more agile, resilient, and customer-focused operations. Below are the key trends shaping the future of manufacturing and setting the stage for the next industrial revolution:
Hyperautomation
Combining AI, robotics, and IoT to create fully autonomous manufacturing systems.Sustainability Focus
Prioritizing green manufacturing practices, such as renewable energy and waste reduction, to meet environmental goals.Customizable Production
On-demand and flexible manufacturing allows businesses to cater to specific consumer needs efficiently.Collaborative Robots (Cobots)
Cobots work alongside human workers, enhancing productivity while ensuring safety and precision.Global Supply Chain Resilience
Smart factories leverage real-time data to adapt to disruptions and ensure consistent delivery of goods.
Building for the Future
The integration of smart technologies in manufacturing is no longer optional; it’s essential for staying competitive. By embracing automation and Industry 4.0 principles, businesses can unlock new levels of efficiency, sustainability, and innovation. The future of manufacturing lies in creating intelligent ecosystems that combine advanced technologies, streamlined operations, and human ingenuity.