3D Printing in Manufacturing: A Catalyst for Innovation
The manufacturing industry, a cornerstone of global progress, has long relied on incremental advancements to meet the demands of a changing world. Yet, every so often, a technology comes along that fundamentally redefines the rules of engagement. Additive manufacturing, commonly known as 3D printing, is one such innovation. What started as a niche technique for prototyping has evolved into a transformative force, reshaping the way products are designed, developed, and delivered across industries.
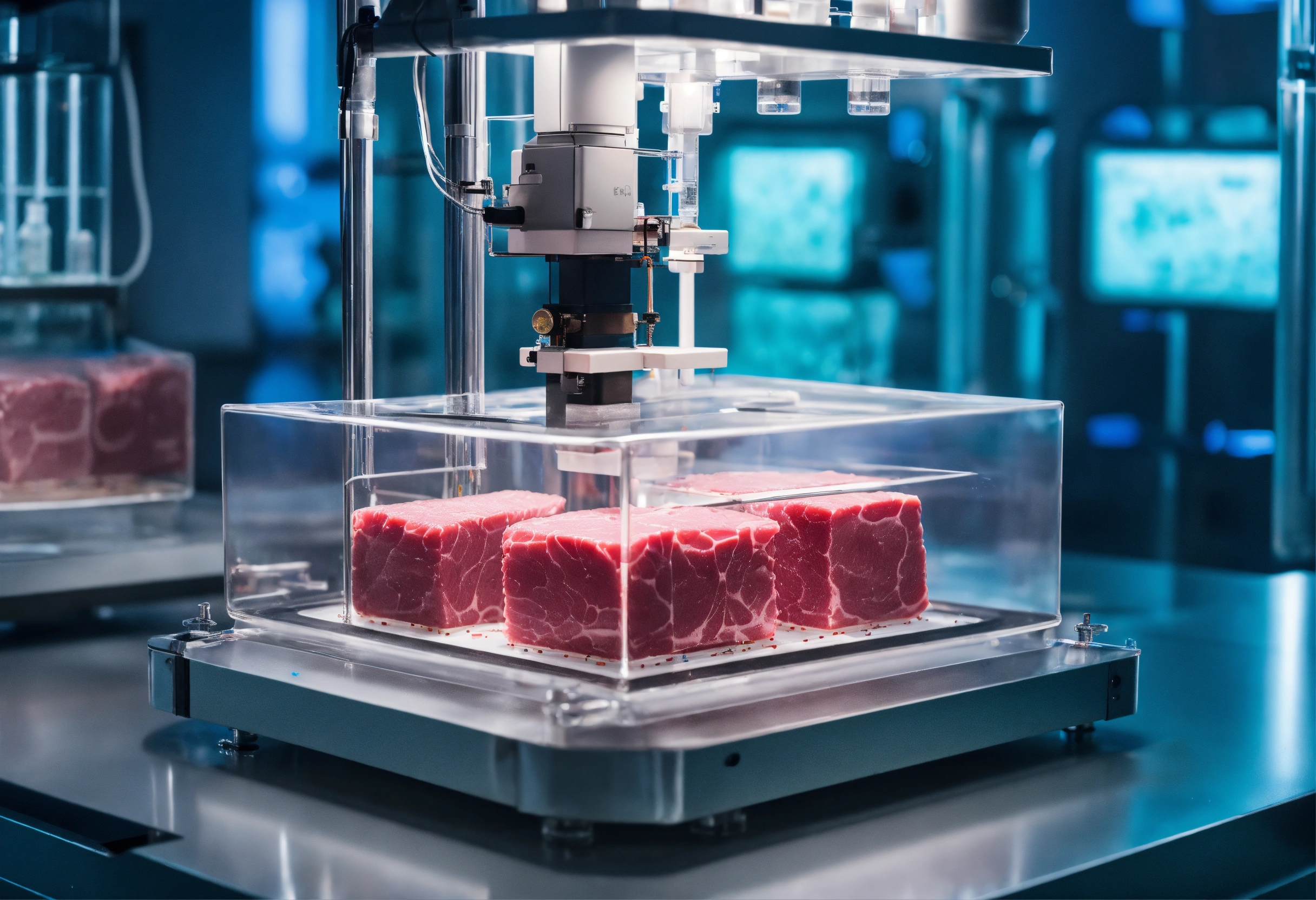
The Origins and Evolution of 3D Printing in Manufacturing
3D printing’s journey began in the 1980s as a tool for rapid prototyping. Early adopters used it to create models and mockups that reduced the time and cost of developing new products. However, the technology was limited by material constraints, slow processing speeds, and high costs. Over the decades, advancements in materials science, hardware, and software have turned these limitations into opportunities.
Today, 3D printing encompasses a wide range of techniques, from stereolithography (SLA) to fused deposition modeling (FDM) and selective laser sintering (SLS). These processes have diversified the materials palette, enabling the creation of everything from aerospace components to medical implants and even consumer goods. But how did it transition from prototyping to production? And more importantly, why is it gaining momentum in critical industries?
Why 3D Printing Matters in Modern Manufacturing
1. Flexibility in Design and Production
Traditional manufacturing often locks designers into rigid frameworks due to the limitations of molds, dies, and machining. 3D printing liberates them from these constraints, enabling the creation of intricate geometries, lightweight structures, and customized designs that would be impossible—or prohibitively expensive—using conventional methods. For instance, aerospace companies now use 3D printing to produce lightweight components with complex internal structures, reducing fuel consumption and emissions.
2. Cost Efficiency in Low-Volume Production
One of 3D printing’s greatest strengths lies in its ability to produce small batches cost-effectively. Unlike traditional manufacturing, which requires significant upfront investment in tooling, 3D printing can produce parts directly from digital files. This flexibility is particularly valuable for industries like healthcare, where bespoke medical devices, prosthetics, and implants are tailored to individual patients.
3. Reduction in Waste
Sustainability is a growing concern across sectors, and 3D printing addresses this by minimizing material waste. Traditional subtractive manufacturing methods often involve cutting away material from a larger block, leading to significant waste. In contrast, additive manufacturing builds objects layer by layer, using only the material required to create the final product.
How Industries Are Leading the Charge
1. Aerospace and Defense
The aerospace industry has embraced 3D printing for its ability to produce lightweight, durable, and complex components. Companies like Boeing and Airbus are using additive manufacturing to create parts that reduce aircraft weight, improve fuel efficiency, and lower costs. For example, GE Aviation’s 3D-printed fuel nozzle, used in its LEAP engines, is a testament to the technology’s potential, combining 20 parts into a single unit and reducing weight by 25%.
2. Healthcare
3D printing has revolutionized the medical field by enabling the production of patient-specific implants, prosthetics, and even bioprinted tissues. Surgeons can now plan complex procedures using 3D-printed anatomical models, improving precision and outcomes. For example, customized cranial implants and orthopedic devices have become commonplace, offering a glimpse into the future of personalized medicine.
3. Consumer Goods
The flexibility and customization offered by 3D printing have caught the attention of consumer goods manufacturers. Companies are using it to produce limited-edition products, custom-fit items like shoes and eyewear, and even experimental designs. Adidas, for instance, has leveraged 3D printing to create its Futurecraft 4D sneakers, which feature midsoles tailored for individual athletes.
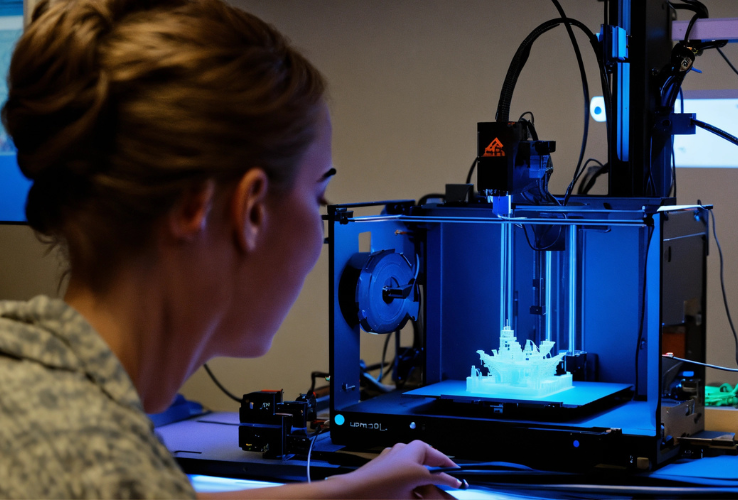
Challenges and the Road Ahead
Despite its advantages, 3D printing is not without challenges. Scalability remains a significant hurdle; while ideal for low-volume production, the technology struggles to compete with traditional methods for mass manufacturing. Material limitations also persist, though ongoing research is expanding the range of options.
Moreover, integrating 3D printing into existing workflows requires significant investment in equipment, training, and digital infrastructure. Manufacturers must adopt a mindset shift, moving from traditional supply chains to more decentralized models that leverage 3D printing’s unique strengths.
Looking ahead, advancements in speed, material diversity, and multi-material printing are likely to further accelerate adoption. Innovations like hybrid manufacturing, which combines additive and subtractive techniques, promise to bridge the gap between 3D printing and traditional methods.
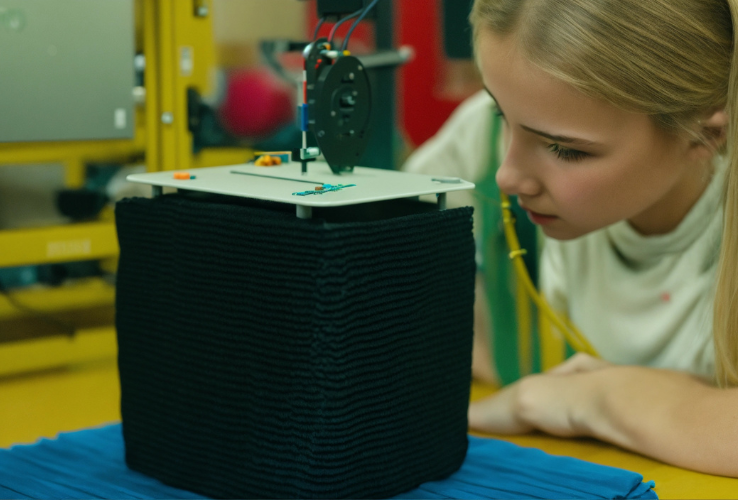
A Catalyst for Innovation and Beyond
3D printing has transitioned from a promising technology to a powerful enabler of innovation. Its ability to merge design and production seamlessly is empowering manufacturers to think beyond the constraints of traditional methods. As industries continue to explore its potential, the question is not whether 3D printing will shape the future of manufacturing but how profoundly it will redefine the rules of the game.
For businesses looking to remain competitive, now is the time to invest in understanding and adopting this transformative technology. The journey may be complex, but the rewards—flexibility, efficiency, and sustainability—make it a path worth pursuing.
In the words of industry leaders, “3D printing is not just about manufacturing; it’s about imagining a future where creativity meets capability, one layer at a time.”